
4 – 20mA Output Signal
2-wire loop powered
The 4-20mA output signal is an analog output signal commonly used in sensors. It is typically powered by DC voltage ranging from 8-32 VDC, which are widely available commercially.
Occasionally, 4-20mA output signals use a three wire configuration (+V, -V, +S), but the vast majority of modern 4-20mA output sensors employ a two-wire, loop powered configuration with a supply (+V) and ground (-V). The current (mA) is measured on the loop by reading the voltage across a known value resistor (often called a sense resistor).
Nearly all industrial level products from Core Sensors offer 4-20mA output options.
Output Signal
4-20mA two wire, loop-powered
Excitation Voltage
10-28VDC
4-20mA Wiring Schematic
How To Guide
For this how to guide, there are three components; power supply, Core Sensors pressure transducer, and a meter or other DAQ system.
1) Power Supply – The first component to the current loop is the power supply, capable of delivering 10-28VDC. The positive (+) terminal of the power supply is connected to the +V pin or wire of the transducer.
2) Core Sensors Pressure Transducer – The -V pin or wire of the transducer is connected to the milliamp input terminal of the meter or DAQ.
3) Meter or other data acquisition (DAQ) – The Common (COM) terminal of the meter or DAQ is then connected to the negative (-) terminal of the power supply. This final step is important as it completes the current loop.
* In certain circumstances, there may be an additional pin or wire used as a case ground. This connection is not critical to the current loop but may be critical to maintain listed certifications of the transducer. Please refer to the Core Sensors wiring guides to verify wiring prior to installation.
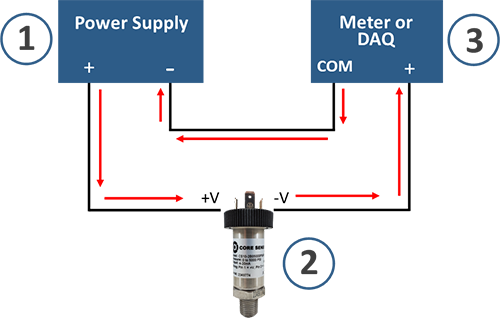
Advantages
- Noise Immunity
- No signal loss over long transmission distances
- Compatibility with various power supplies and PLC’s because of high usage in general industry
Disadvantages
- Current consumption is high when compared to a voltage output sensor
- Need for at least 10VDC excitation, making for limited battery-powered options
Millivolt Output Signal
The millivolt output signal is the oldest signal, yet still has popular uses today. Sensors with millivolt output can be roughly separated into two categories; compensated and uncompensated. Compensated sensors are generally ones where the output has been trimmed with resistors to have a set zero and span tolerance, along with a specific sensitivity (commonly 5 or 10mV/V) over a specified temperature range such as 0-55°C. Uncompensated millivolt output is generally the raw output of the sensor that has not been adjusted or trimmed, and is usually stated with a typical output range, such as 100mV output, +/-25mV @ 10VDC excitation. With either choice, one common advantage of millivolt output is the response time to changes in pressure. The frequency response time of millivolt output sensors is fast because there are no circuits to slow down the signal changes.
Choosing compensated vs uncompensated depends on the needs of the application. If the application includes a signal conditioner that simply amplifies the sensor output, compensated is usually the better choice because the sensor is already set to meet published performance over a specified temperature range. If the application is one where the equipment will be characterized and compensated/error corrected as a whole using a signal conditioner that can set zero, span, and temperature compensation, an uncompensated output is a good choice because it maximizes that output available for adjustments and error correction.
In physical terms, one of the primary advantages of millivolt output sensors is size and packaging flexibility. Because there are no ICs and other large electronic chips to fit inside the sensor housing, millivolt sensors are more flexible in design to fit into embedded systems and customized equipment.
Millivolt Wiring Schematic
How To Guide
For this how to guide, we have three components; power supply (labeled as 1 in the schematic), Core Sensors pressure transducer, and a meter or other DAQ system (labeled as 2 in the schematic).
1) Power Supply – Connect the positive (+) terminal of the power supply to the +V pin or wire of the transducer. Connect the negative (-) terminal of the power supply to the Ground (GND) pin or wire of the transducer.
2) Meter or other data acquisition (DAQ) – Connect the COM terminal of the meter of DAQ to the -Signal pin or wire of the transducer. Connect the Volts input terminal of the meter or DAQ to the +Signal pin or wire of the transducer.
This will complete the 4-wire circuit.
* In certain circumstances, there may be an additional pin or wire used as a case ground. This connection is not critical to the output signal but may be critical to maintain listed certifications of the transducer. Please refer to the Core Sensors wiring guides to verify wiring prior to installation.
Advantages
- Noise resistance due to lack of ICs.
- Fast response time to changes in pressure.
- Perfectly ratiometric, so any power supply will work (up to the max VDC)
- Flexible design possibilities for embedded systems
Disadvantages
- Requires 4-wire connection
- Possible low signal to noise ratio in applications where EMI/RFI is present
- Limitations on signal transmission distances
- Often requires external/additional signal conditioner
Common Applications
High Performance Liquid Chromatography (HPLC) – mV sensors are common in HPLC because often the system and pumps are calibrated as a whole and/or the system already has an on-board signal conditioner with trimming features to re-calibrate the equipment when needed. Also, mV sensors can be made as custom embedded units more easily, resulting in lower “dead volume”, which is important in HPLC applications to reduce cross-sample contamination.
Mass Flow Controllers (MFC) – Use of mV sensors in MFCs is common for similar reasons as the HPLC, with the additional need for fast response time. The fast response time of mV sensors in the MFC is vital to fine tune the amount of product that is allowed to flow into the process.
Scales and weighing equipment/hydraulic press and forming – mV sensors are used in hydraulic weighing and machine press applications to replace load cells. The mV output of the sensors is similar to the mV output of many load cells, allowing OEMs to minimize system redesign when upgrading from a load cell to a pressure sensor.
Higher ambient temperature applications – In applications such as super-heated steam, downhole drilling and MWD, or applications measuring pressure in a engine compartment of a moving or stationary engine, temperatures can climb to a range that is not compatible with ICs and ASICs. Because of the lack of ICs, mV units can generally be installed in locations that are simply too hot for amplified sensors, and the signal is transmitted to a remote signal conditioner. The CS-HTP high temperature pressure sensor and CS-90 downhole pressure sensor are recommended for applications where high temperatures are a concern.
Heating, Ventilation, Air Conditioning, and Refrigeration (HVAC/R) – There are numerous applications in HVAC/R systems where pressure is measured. Often, there is a need for two separate sensors to be used to measure pressure in two spots to provide operators with the differential pressure reading. These PLCs are designed to accept two mV signals and report the differential pressure. The CS10 industrial pressure transducer with a millivolt output signal would be an ideal solution to handle this type of application.
Voltage Output Signal
1-5V, 1-6V, 0-5V, 0-10V, 0.5-4.5V, 0.5-2.5V
A voltage output signal is an analog output signal commonly used in pressure, temperature, and other types of sensors. Within the realm of voltage output, there are a variety of I/O options, including the ones in the table below.
The most common voltage output signals, especially where power consumption is not an overriding consideration, are 1-5VDC, 1-6VDC and 0-10VDC for industrial applications.
With the growth of IoT & IIoT projects that incorporate sensors, the capability to operate from low power with less current consumption is valuable, especially for equipment being deployed in remote areas where frequent battery changes are costly and time consuming.
To address low power needs, there are a number of voltage output options that can be powered from 3V, 3.3V, 3.7V, 5V, and 9V power supplies and batteries. The voltage output signals commonly paired with these supply voltages are*: millivolt, 0.5-2.5VDC non-ratiometric and 0.5-4.5VDC ratiometric. The option for 0.5-2.5VDC output is rapidly growing in popularity because of the increased use of 3 to 5VDC lithium ion batteries.
*See table for excitation voltage requirements.
While the millivolt signal is a ratiometric signal, the term ratiometric is most commonly paired with 0.5-4.5VDC output, which is ratiometric to a regulated 5VDC excitation. The ratiometric output signal 0.5-4.5V output signal became widely popular in automotive and off-road applications. With vehicles using a 12V supply, users could regulate the voltage down to 5V, and create a signal that is proportional to the supply. A 10% reduction in supply from the 5V supply creates a proportional 10% decrease in the output signal. It is still used in similar applications and has also been utilized in industrial applications such as compressors and water pumps.
Output Signal |
---|
0-5VDC, three wire |
0-10VDC, three wire |
1-5VDC, 1-6VDC |
0.25 to 10VDC, 1-10VDC |
0.5-4.5VDC, ratiometric |
0.5-2.5VDC, non-ratiometric |
Excitation Voltage |
---|
10-28VDC, unregulated |
15-28VDC, unregulated |
10-28VDC, unregulated |
15-28VDC, unregulated |
5.0VDC, regulated |
3-5VDC, unregulated |
3-Wire Voltage Wiring Schematic
How To Guide
For this how to guide, we have three components; power supply, Core Sensors pressure transducer, and a meter or other DAQ system.
1) Power Supply – Connect the positive (+) terminal of the power supply to the +V pin or wire of the transducer. Connect the negative (-) terminal of the power supply to both the Ground (GND) pin or wire of the transducer and the Common (COM) terminal of the meter or DAQ. If using a bench test setup, this is commonly done by using a male to male banana plug to connect the power supply and meter and stacking a banana to alligator clip to connect the power supply to the transducer.
2) Meter or other data acquisition (DAQ) – Connect the Volts input terminal of the meter or DAQ to the Signal pin or wire of the transducer.
* In certain circumstances, there may be an additional pin or wire used as a case ground. This connection is not critical to the output signal but may be critical to maintain listed certifications of the transducer. Please refer to Core Sensors wiring guides to verify wiring prior to installation.
Advantages
- Many signal configurations to fit a variety of electronics options, power supplies and PLCs
- Low-power, low current consumption options
- “Live Zero” options improve troubleshooting support (for example, no power vs system/sensor failure)
Disadvantages
- Long cable runs can lead to signal attenuation/signal loss
- Does not have the level of noise immunity as 4-20mA current output
Common Applications
Tank Level Monitoring – For tank level applications, a voltage output pressure sensor with an IP-68 rating can be packaged with a SCADA system to remotely monitor fuel or water level for remote installations requiring low current consumption due to battery life concerns. The CS12 Submersible Pressure Transducer and CS82 Intrinsically Safe Submersible Pressure Transducers can be manufactured with a low current consumption ASIC to perform in this application.
Oil Field Equipment – In remote oilfields, voltage output pressure sensors and temperature sensors consume less battery life while providing enough signal to measure the media and transmit the signal to the telemetry unit. Data is then sent to the cloud for analysis and monitoring.
IIoT – Industrial applications continue to take advantage of IoT technology. Factories are measuring pressure and temperatures of test equipment as well as automation equipment to maximize efficiency, especially in locations where it is too costly or difficult to run power.
HVAC and Refrigeration – Voltage output signals continue to be a popular option amongst HVAC/R OEM and service installations. Due to the low cost and ease of use, pressure, temperature, and combination sensors can all be quickly integrated with noise immunity within the commonly short distances where sensors are run in HVAC automation applications, such as boiler rooms. Products such as the CS10 Industrial Pressure Transducer can be designed with a voltage output signal for low to high volume applications.
The above information has been kindly provided by Core Sensors and taken from their official website, links for which can be found below.
Millivolt Output Signal Pressure Sensors | Core Sensors (core-sensors.com)
Voltage Output Pressure | Temperature | Level Sensors – Core Sensors (core-sensors.com)
4-20mA Output Signal | Core Sensors (core-sensors.com)
-
Wiring Guide - Solder Hooks
Download -
Wiring Guide - Turck Lokfast M12
Download -
Wiring Guide - Turck Minifast
Download -
Wiring Guide - 6-Pin Bayonet/Bendix
Download -
Wiring Guide - Deutsch DT04-4P
Download -
Wiring Guide - Deutsch DT04-3P
Download -
Wiring Guide - Mini-DIN 43650 Form C
Download -
Wiring Guide - DIN 43650 Form A
Download -
Wiring Guide - Packard Metripack 150
Download -
Wiring Guide - M12x1 Eurofast
Download -
Wiring Guide - Flying Leads/Wires
Download -
Wiring Guide - Standard Cable
Download